LATEST FIREARM NEWS FROM ALL BRANDS
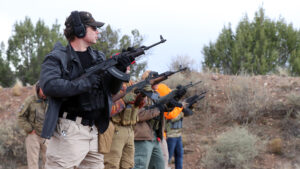
Readying for Red October: Gunsite AK Armorer-Operator Course
Robert Jordan April 26, 2024
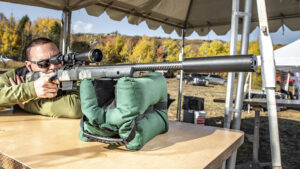
VIDEO: Testing the Hunt-Ready Silencer Central Buck 30 Suppressor
Andy Grossman April 26, 2024
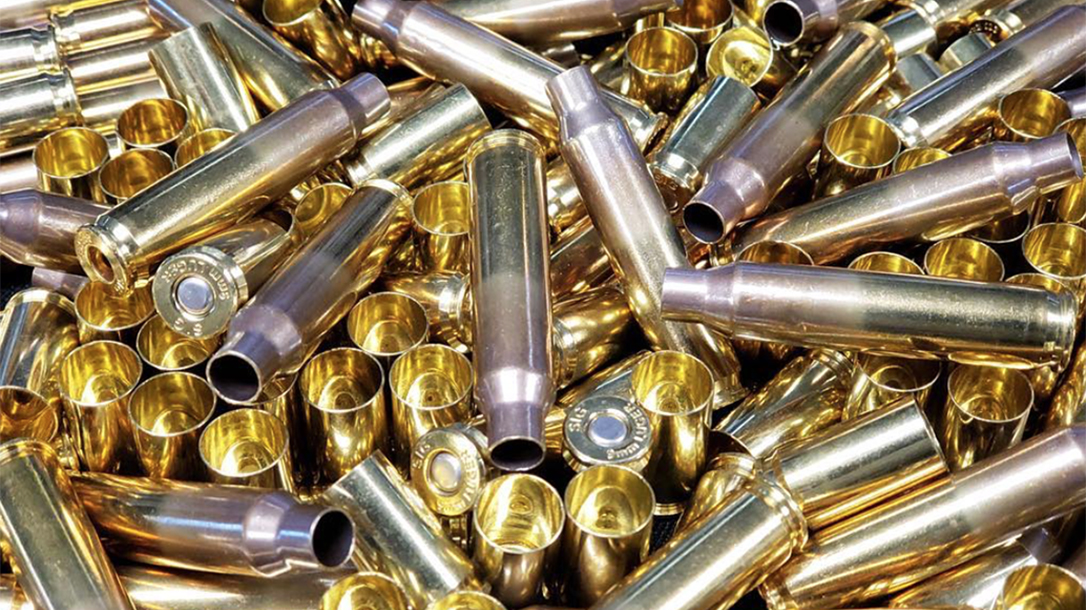
SHOOTING 101: Understanding Ammunition Types & Function
Mark Chesnut April 25, 2024
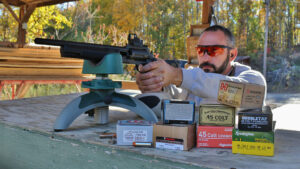
Ammo Match: .45 Colt Shows Its Versatility with These Eight Cartridges
Frank Melloni, Freelance Ammunition Editor April 25, 2024
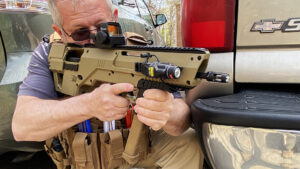
Meta Tactical Apex Conversion Kit: Pistol to Carbine in Minutes!
Frank Jardim April 24, 2024
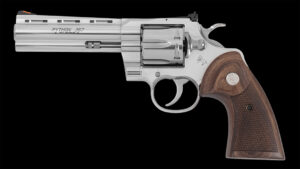
Colt Python Revolvers: 2.5 & 5-inch Stainless Steel Models Debut
Ballistic Staff April 23, 2024
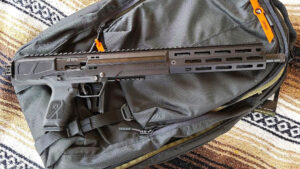
Versatility Defined: Shooting the Well-Rounded Ruger LC Carbine 45
Mike Detty April 23, 2024
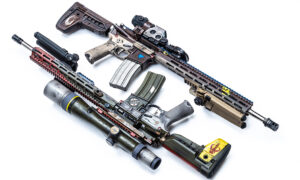
BLACK RIFLE BUILD-OFF
Athlon Outdoors Staff April 23, 2024
BROWSE BY BRAND
Didn't find what you were looking for?
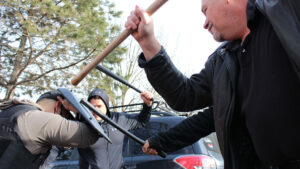
Combatives: Training in Reality-Based Self-Defense for the Street
Waysun Johnny Tsai April 24, 2024
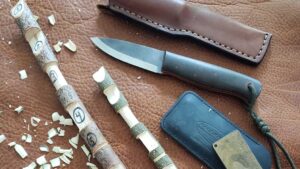
How To Make A Bushcraft Try Stick
Kevin Estela April 23, 2024
CHECK OUT ATHLON OUTDOORS ORIGINAL VIDEO SERIES
More Videos
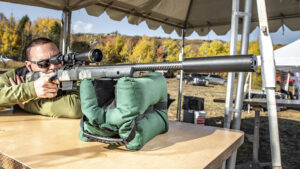
VIDEO: Testing the Hunt-Ready Silencer Central Buck 30 Suppressor
Andy Grossman April 26, 2024
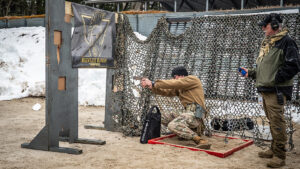
West Point Wins 4th Consecutive SIG Relentless Warrior Championship
Tactical Life Staff April 22, 2024
Tests and Product Reviews
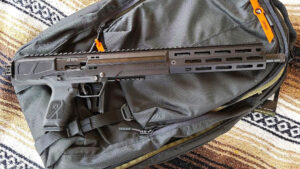
Versatility Defined: Shooting the Well-Rounded Ruger LC Carbine 45
Mike Detty April 23, 2024
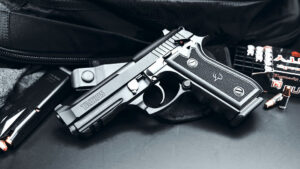
TESTED: Taurus 917C DA/SA 9mm Pistol Upgrades an Old Favorite
Mike Detty April 18, 2024
SUPPRESSORS & NIGHT VISION

VIDEO: Testing the Hunt-Ready Silencer Central Buck 30 Suppressor
Andy Grossman April 26, 2024
The fact we were able to make so much noise in the middle of a potato field in Idaho at a media event, when there were so many suppressors on guns, was honestly incredible. I’m talking about the best media

Maxim Defense Expands the PDX-SD with 7.62x39mm and .300 BLK Options
Personal Defense World April 12, 2024
In 2019, Maxim Defense introduced its short and maneuverable PDX short-barreled PDW, followed one year later by the PDX-SD. The PDX-SD expanded on the original platform by adding an integrated suppressor while maintaining stealthy, close-quarters handling. However, although the original
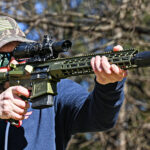
Huxwrx Ventum 762: Hub-Compatible Flow-Through Suppressor
Andy Grossman March 6, 2024
One of my favorite things about being in the outdoor industry is media events. I love seeing new products before companies release them to the public. Even cooler, companies sometimes ask for my thoughts on a product as a shooter.

VIDEO: Testing the Hunt-Ready Silencer Central Buck 30 Suppressor
Andy Grossman April 26, 2024

Maxim Defense Expands the PDX-SD with 7.62x39mm and .300 BLK Options
Personal Defense World April 12, 2024
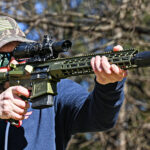
Huxwrx Ventum 762: Hub-Compatible Flow-Through Suppressor
Andy Grossman March 6, 2024
Didn't find what you were looking for?

Drawing From a Holster Pistol Drill: Draw to First Shot on Target
Kenzie Fitzpatrick April 22, 2024
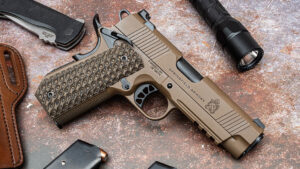
Springfield Armory TRP Carry Contour Review: The Concealable 1911
Garrett Lucas April 11, 2024
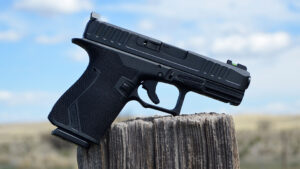
Running the ZRO Delta FKS-9: The Glock Clone Living on the Edge
Mike Detty April 8, 2024